Construction Management - Why Logistics is so Important
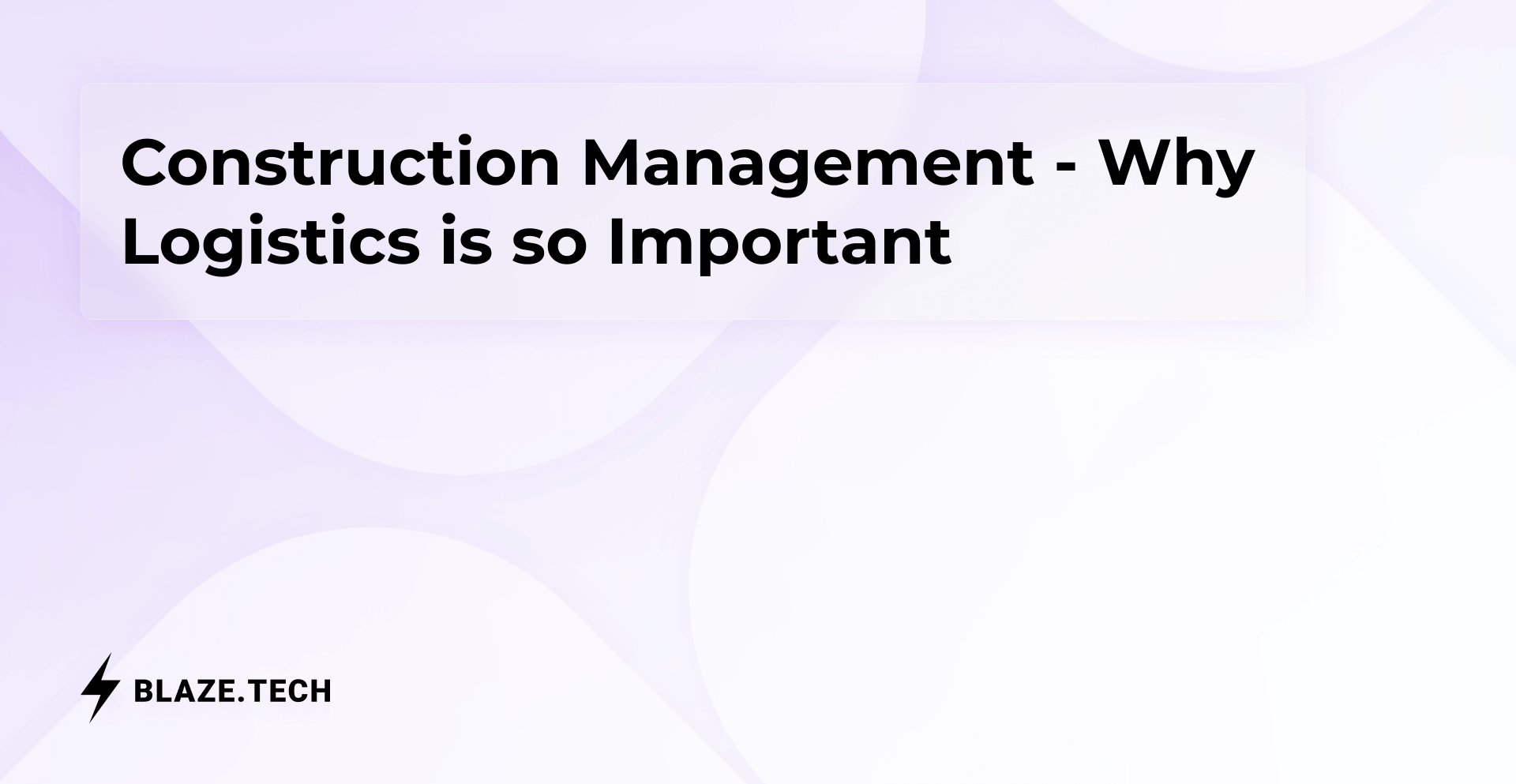
“Amateurs study tactics; professionals study logistics.”
The saying above is military in origin, but it also applies to the construction industry. For just like a military campaign will collapse if it cannot maintain its supply lines, so too does a construction project depend on carefully managed planning and timely deliveries of people and materials. Delays in any part of a project can have a ripple effect on other parts, slowing overall progress and increasing costs. Project disruptions and rescheduling can lead to financial and reputational harm for contractors, especially if the delay was avoidable.
In this article we discuss logistics as they apply to construction contractors. We will also see how digitization advances in no-code application development offer small and medium-size construction contractors a practical and affordable way to integrate and improve your logistics in all areas of construction planning and execution.
What are “Logistics?”
Fundamentally, logistics are how we plan, prepare for, and manage the execution of an activity. At this simple level, almost anything we do involves logistics. Even making a peanut butter sandwich requires some planning and materials delivery in advance; without bread, for example, the process soon comes to a halt and remains stalled until the bottleneck can be fixed.
What can make logistics hard to understand is that when they are working properly, they are often invisible to project shareholders and end users. Logistical failures, however, are often highly noticeable because of their ripple effects on things people can readily see like efficiency, economy, safety, quality, reliability, and timeliness. For example, if you fly on a plane, you may not think about the logistical effort needed to keep its engines in good working order – until one of them breaks down in midflight because a critical part replacement had to be delayed because of a delivery error. Then you notice.
For purposes, it is helpful to think of logistics as the behind-the-scenes work that goes into planning, preparing for, and efficiently sustaining through timely completion a multi-party effort to take an idea from blueprint to reality – a complex construction project, in other words.
How do Logistics Apply in Construction?
No single definition of construction logistics exists. Here are a couple of ways that some have expressed it:
“Construction logistics is planning and managing logistical services, vehicles, and the workforce involved in a construction project.”
“Logistics in construction management is the process of planning, executing, and controlling procurement, transportation, workers, and resources.”
The key concepts to remember are planning and managing. Project execution is a function of leadership by the contractor. Logistics are what support that execution.
With rare exceptions, like the airplane engine example above, logistics failures seldom result in catastrophic failures but instead take a toll on project efficiency, worker productivity, and construction budgets. Inadequate planning, poor material management, schedule slips, incomplete documentation, design process errors, difficulties responding to owner-requested revisions, payment delays, and inefficient management of contractors and suppliers are all reasons why only about one-third of construction projects stay within 10 percent of budget – and all are aspects that a good construction logistics plan should account for.
With this in mind, then, let us consider the specifics of what goes into effective construction logistics.
Logistics Apply to all Parts of a Construction Project
Because construction projects often involve multiple contractors and laborers who participate in different ways and at different times, it is easy for some of them to see logistics from their own limited perspective instead of as a whole. For example, some refer to construction logistics as involving site support activities, like maintaining site security and orderliness. These we can call site logistics. Others think of construction logistics in terms of resource and inventory management, making sure that construction materials make it to the job site on time and in the needed amounts.
It may be better, though, to think of these logistical considerations as being under the umbrella of construction logistics, a scope that encompasses and coordinates the movements and activities of all people, materials, and work schedules connected with the project.
Consider, for example, the planning and management that goes into building something as “simple” as a single-family residence. There are structural elements, like the foundation, the frame, the floor, and the roof; functional elements including doors, windows, electrical wiring and hookup, plumbing, heating, and air conditioning; and finishing elements such as drywall, paint, sidings, gutters, countertops, interior finish carpentry, and more.
Behind many of these elements you can find more logistical contributors like material suppliers, architects, designers, landscapers, and even government agencies and employees connected with permitting, inspections, and final approvals. In short, there is little within the planning and execution of any construction project that is unaffected by construction logistics.
Logistics Apply to all Phases of Construction
Successful construction logistics managers must account for more than all the parts and the people who come together on the site. The timing of when they work how they coordinate with each other is also important. The same single-family residence we mention above does not come together all at once but in sequential phases: plans and permit acquisitions, site work and masonry, framing, electrical and plumbing, flooring, insulation, and drywall installation, and lastly exterior finishing and landscaping. It is as logistically unsound to schedule the electrician before the framing is complete as it is to seek a construction permit after the drywallers have just finished up.
Bad logistics on one project can lead to supply bottlenecks, delays, idle workers, subcontractor schedule conflicts, inspection failures, quality control problems, avoidable change orders and cost overruns, or even a lawsuit against the contractor. Bad logistics as a practice can do enough reputational and profitability harm to put a contractor out of business. In contrast, intelligent logistics practices make for good business because they help keep everyone and everything involved with the project appearing and working in the right place and time.
What Goes into a Construction Logistics Plan?
Now that we can appreciate the importance of construction logistics, we can identify the elements of an adequate logistical plan to streamline the construction process, maximize worker productivity, and maintain quality assurance. Here are some specific plan elements for logistics professionals to think about:
- Site preparation. Will any grading, excavation, or demolition be needed before construction begins?
- Industry standards and safety regulations, including risk management.
- Construction site traffic flow. Transportation of personnel, equipment, and materials to the project site. What materials and equipment are needed at each stage of the project? What kinds of transport will be used? Where are the locations to unload these items? Is the site infrastructure adequate to handle the transportation needs?
- Equipment maintenance.
- Waste management.
- Managing subcontractors and suppliers, and project benchmark tracking. How often and when are deliverables scheduled?
- Onsite and offsite material fabrication and use of storage centers.
- Site security and application security for hardware and software used on the project.
Using Low-Code and No-Code Software Tools in Construction Logistics
Planning is the most serious challenge to construction project logistics, because often no two projects are alike. It is also common for requirements and plans to change as work on the project comes along.
The construction industry has been hesitant until now to embrace the latest technology and digital processes available, in part because of their cost, complexity, and the difficulty in customizing them to unique project logistical needs. But in today’s highly cost competitive construction supply chain ecosystem, a key trend for the construction logistics market is to maximize efficiencies in every part and phase of the job. To achieve timely results, everything about the project must be planned: material supply, labor availability, transportation of people and equipment, and more. Construction project management software can provide a central platform for project material and resource management, but it must be responsive to the needs of construction managers everywhere they go, not only in the office but also on the construction site.
In this regard, contractors using low-code or better yet no-code software now have a practical way create digital logistical tools suited to their specific needs. With a low-code or no-code construction logistics software package, it is not necessary to rely on a software programmer to build a consolidated, dashboard-based application that includes features for workflow tracking, resource and inventory management, contract and other document management, payroll management, risk management, materials and delivery scheduling, hours tracking, building code compliance, and whatever else you need.
Try Blaze Today for Your Construction Logistics Needs
Construction site logistics is a complex yet crucial piece of efficient construction practices. Without sound logistical processes in place, it would be impossible to complete projects on time, within budget, and according to the owner’s specifications. Having a comprehensive yet flexible and customizable construction logistics plan is essential to successful project completion no matter the project size.
Because construction supply chains and other logistical processes are transforming with the availability of new software technology, to remain profitable and competitive construction industry logistics managers must stay current with the latest and most efficient digital processes, minimizing the risks of bottlenecks and reworks while streamlining coordination among all members of the project team.
A no-code construction project management software solution you build using Blaze gives you the power and flexibility to create construction logistics plans. You can also quickly, easily, and affordably adapt your logistics apps to each construction project you manage as a contractor. No need to hire outside logistical consultants. No need to pay for costly software programmers to write lines of code just to make a minor change to your logistics plan. You can get started for as little as $25/month/user, with enterprise-level growth and customization options available to match even the most detailed requirements for your construction business.
Questions? Contact us online and one of our team members will answer them for you. Or, if you are ready to see just what Blaze can do for your construction logistics needs, you can request a demonstration here.
Latest Blog & News
We love what we do and are creating a variety of resources to make you a superhero on your team! Read our articles to get inspired with what you can build with Blaze.

How to Build a Dashboard Management System Without Coding

Top EHR for Therapists and Mental Health Professionals in 2025
