Guide to Construction Management Procurement | Blaze
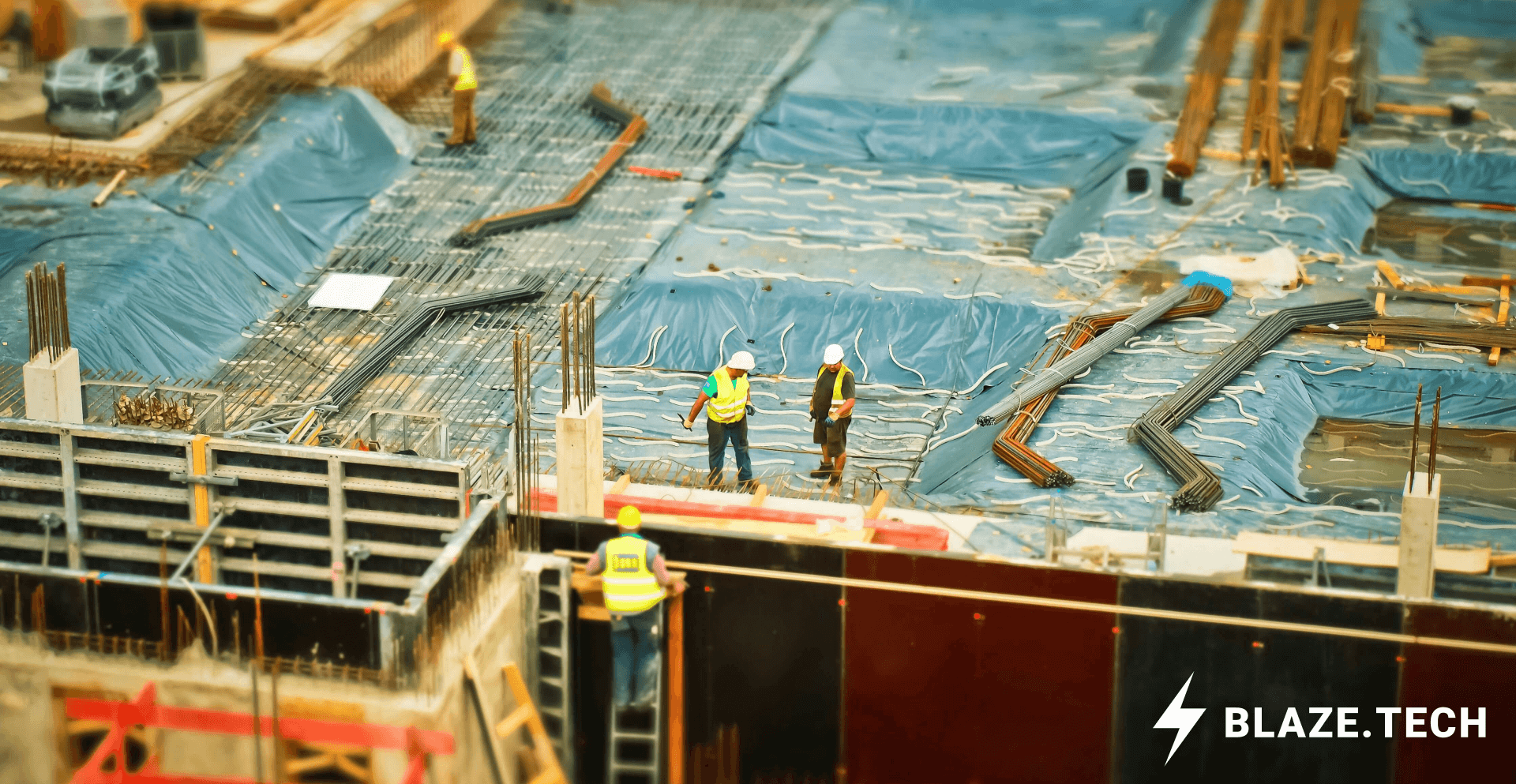
Every human creation, no matter how simple or complex, begins as an idea. Similarly, every structure you see around you, whether an office building, a school, or a single-family home, began its existence as a collection of materials on a job site and a gathering of people there to assemble them into something greater. The necessary process of bringing these materials and people together at the right time is, in the larger sense, what construction logistics is about. And within the sphere of logistics, making sure that everything needed at the site gets there on time and within budget is the purpose of construction procurement management.
What is construction procurement?
Construction procurement describes what goes into acquiring materials and services to use in a construction project. Although simple on its face, there is more to construction procurement than simply buying or renting things for the construction site. In this article we take a detailed look at what goes into efficient construction procurement, how contractors and project managers plan and organize it, and some ways that you can use modern, no-code software to make your construction procurement more cost effective.
Where does construction procurement fit into a construction project?
We can think of a construction project in terms of layers. The highest layer is project management, where the overall project planning happens. Beneath that layer is construction logistics, in which the project manager arranges for the on-schedule delivery of people, equipment, and materials to the construction site. Construction procurement is the actual acquisition of the materials required for the construction logistics to work properly.
What goes into managing construction procurement?
The two most fundamental aspects of construction procurement management are financial and quality considerations. Financial considerations include budgeting, costs, and managing any payment financial terms. Quality considerations involve the quality of materials and the timeliness of their delivery. For some projects, like ones that involve overseas bidding, you may also need to plan for additional environmental, social, and governance (ESG) requirements.
Throughout a project lifespan, construction procurement management touches on the following aspects:
- Identifying, negotiating with, and contracting with vendors, and maintaining procurement-related documentation.
- Site scheduling for personnel and sourcing of materials, including lead times and slippage allowances.
- Coordinating and communicating with the project manager and logistics manager to continuously monitor procurement progress and to react to developments that could affect labor and material costs, availability, and quality.
What does a construction procurement manager do?
Managing construction procurement is ultimately the responsibility of the construction project manager. On smaller projects the project manager will often retain and exercise direct authority over procurement. On larger projects, though, it can be more efficient for the project manager to delegate procurement authority to a construction procurement manager. Sometimes the construction procurement manager may report to a project logistics manager, who in turn reports to the project manager.
Regardless of who must handle them, construction procurement responsibilities commonly cover five main areas: procurement planning, schedule management, contract management, project monitoring, and risk management. Let’s take a closer look at each below.
Procurement planning
Not every building operation flows smoothly through all its stages of planning, construction, inspections, and completion. Problems with project scope increases, scheduling changes, and other possible disruptions can and do arise with suppliers, and these can threaten to delay the work, increase costs, or both. Project logistics should take these variables in procurement as part of the strategic procurement plan. This includes building time into the procurement plan to allow for schedule pushouts, and to pre-identify and, if necessary, call upon back-up suppliers.
Schedule management
Like procurement planning management, procurement scheduling management is an integral part of project logistics, which controls the overall timing and delivery of people and materials to the job site. The procurement manager needs to regularly and continuously coordinate with the project manager or the logistics manager to coordinate the activities of the procurement team with the project completion schedule, so the supplies and services needed under the logistics plan are in place when and where they need to be.
Contract management
Construction project purchases frequently involve negotiating and overseeing fixed cost or cost-reimbursement contracts with subcontractors, suppliers, and other vendors to purchase or lease equipment, materials, and services. This in turn involves pre-contract activities including issuing requests for proposals, evaluating proposal bids, and selecting which suppliers and servicers to work with.
Project monitoring
Once the contracts are finalized, the construction procurement manager must then follow the performance of each contract to completion, including cost-effective and timely responses to the need for change orders. If a problem happens during contract performance, the procurement manager guides the process of resolving the issue, including coordinating with the project manager and with legal counsel if necessary. Lastly, procurement contract management includes closing out contracts as they are completed.
Risk management
Risk management in construction procurement has passive and active elements. When you exercise control over those parts of the construction process like procurement planning, deliveries scheduling, and contract management, this has the indirect and beneficial side effect of lowering the risk of problems happening in these areas. Active risk management measures are those you take for that specific purpose. These can include doing credit checks on suppliers, especially during the bidding process, and visiting bid candidates to ensure that they can deliver on their promises of performance.
What kinds of construction procurement exist?
The methods of procurement in the construction industry vary, depending on the project size, complexity, and location. The method you use for a rural single family home renovation project may be different from what you use for an urban multi-use development. Here are some of the more common types of construction procurement methods you might encounter on a project:
- Design-Bid-Build. In this method, the owner and the architect work together to design the project then the owner solicits fixed-fee bids from contractors.
- Design-and-Build. The Design and Build method has the owner negotiate with the contractor to design and build the project. This eliminates the preliminary coordination between the owner and architect common in the Design-Bid-Build process.
- Management Contract. Used commonly on larger construction projects, this procurement method relies on the owner contracting with multiple contractors under a managing contractor, who serves as the project lead for overall project management and design.
- Construction Management. This method is like the Construction Management one above, except that instead of contracting directly with the contractors the owner designates a fixed-fee management team to oversee the procurement process.
- Joint Venture. In the Joint Venture procurement method, procurement control and accountability are the responsibility of a joint venture management team.
What are the benefits of optimizing construction procurement?
The advantages of making the best use of your construction procurement system can be hard to see by themselves because they are indirect in their effects. Taken together, though, these advantages can make the difference between a smoothly-run project that is on time and within budget and one that gets out of control. Here are four ways how you can improve your project performance, and your bottom line, through better construction procurement processes:
- Better communication. Effective communication among construction project management, project logistics management, and project procurement management is the bedrock of taking a project from a blueprint to completion. None of these three managers can succeed coordinating with the other two, so it is essential that they work together. This is particularly relevant to risk minimization and budget preservation: the earlier the project manager learns of a development that could affect scheduling or budget, the sooner and more effectively the entire management team can adapt to it and where possible mitigate its effects.
- Timely acquisitions and deliveries. Integrating procurement scheduling into logistics management planning means improving the likelihood that the continual choreography of construction – the gathering of contractors, subcontractors, laborers, and materials – will be as seamless as possible, day after day.
- Risk minimization. The same careful planning and coordination that goes into efficient procurement scheduling creates the positive side effect of reducing procurement and logistical risks. By anticipating and preparing for possible labor and material procurement choke points, construction procurement management reduces the possibility of labor and material shortages, unexpected price increases, and scheduling delays.
- Improved budgeting. Construction project budget control has two parts: negotiating the best prices for labor and materials to go into the project, and keeping the need to make planning, logistical, and procurement changes to a minimum. A construction procurement manager with enough depth of knowledge and experience to understand the market availability and prevailing costs of the services and items to be purchased can better avoid paying too much for them and can quickly switch to alternative supply sources if the need occurs.
Project management software in construction procurement
Without clear communications and effective coordination among all the participants in a construction project, cracks can appear in the project planning and execution that, if not addressed promptly, can lead to schedule conflicts, misunderstandings and mistakes, project delays, needless change orders, increased costs, and lost profits. It follows, then, that a tool that simplifies and centralizes the construction procurement process can reduce these risks and foster smooth project logistics.
Having a construction procurement management system that integrates as seamlessly as possible with the overall project management plan supports project success. It helps the procurement manager to maintain construction quality control, to respond promptly to forecast changes on the construction site, to communicate effectively with the other project team members and with material and service suppliers.
Software tools already exist that generally support procurement technology. These provide features that can include consolidated, live dashboards, Kanban boards for project teams, Gantt charts, and many kinds of reporting views and filters. But while these applications are an improvement over paper-based project management, their application to construction management generally and to construction procurement in particular can be limited. For example, the same generic project management software that supports a marketing campaign, social event planning, or a new product launch might not be wholly suitable to managing construction logistical and procurement tasks like supplier cost analyses, coordinated scheduling with other project contributors, near real-time communications, and budget monitoring throughout the life of the project.
No-code applications for managing construction procurement
Until recently, adapting generic software applications for specific purposes by making changes to application programs – like configuring a vanilla project management system into one customized specifically for construction procurement management – was too costly, too complicated, or both. Some application packages have evolved from the old, programmer-centric “high-code” way of modifying applications to a “low-code” approach, but while being less expensive than high-code programming this approach still relies on template-based and other preconfigured workarounds to build a customized application that still might not be exactly what you need.
The latest advances in software application technology have led to new, no-code development approaches that avoid the need for software programmers to modify applications for you. They also make it easier to build fully customized applications yourself than low-code options do. By using a no-code solution you do not need to have any training as a software developer or engineer to create your own applications. You can build a construction procurement management application in minutes that can connect with any supplier data source, communicate with and synchronize with other construction project management and scheduling applications, specify user permissions, manage contracts, and track supplier deliveries. You can take an older, paper-based construction procurement system and digitize it.
In short, when you use a no-code construction solution, not just with procurement but for any aspect of construction planning and execution, then “If you can describe it, you can build it.” Forms. Tables. Workflows. Dashboards. Data analytics and reports. Supplier and delivery management. Document control and change tracking. When you use a no-code application development solution like Blaze, you can even build multiple applications for all aspects of construction project planning and management – not just procurement but also logistics, employee hiring, supervision, and compensation, and more – and link them together into a single yet modular whole that work together perfectly because they share the same programming source.
Key Takeaways
Whether you manage it well or poorly, your control over construction procurement is one of the easiest ways to gauge your overall construction project management. Manage your supplier and deliveries well, and you will see projects through from planning to completion with minimal need for pushouts and change orders because of late deliveries to the site. Fail to do so, and you might experience project delays, cost increases, workflow inefficiencies, idle laborers, and unhappy owners. If you gain a reputation for sloppiness in procurement planning and execution, it can harm your business profitability or even threaten its survival.
Having the best construction procurement management tools available, and better yet having software tools that suit your needs exactly because you can easily and affordably create them yourself, might not guarantee project success. But using no-code applications you build through Blaze to maximize your procurement efficiency can certainly improve your chances of success. And if you need help getting started, expert help is available to you online.
Ready to begin building your own construction procurement management application? A good way to get started is to request a Blaze demo. There is no better way to learn what we can do for you than to see for yourself.
Do you still have questions about how to use no-code software in your construction project? We have answers for you. You can contact us directly through our website, or if you prefer you can send us an email.
Latest Blog & News
We love what we do and are creating a variety of resources to make you a superhero on your team! Read our articles to get inspired with what you can build with Blaze.

How To Build Back Office Applications With No-Code Tools

FlutterFlow Review 2025: Pros, Cons & Pricing
